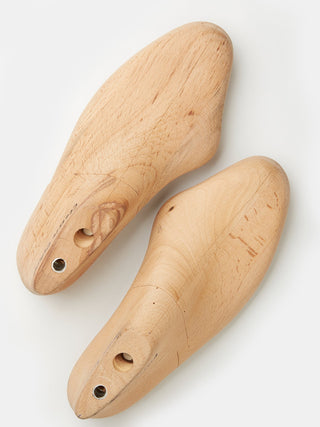
Bespoke
Arthur Sleep has brought bespoke shoemaking and manufacturing back to central London. Using traditional techniques and materials alongside modern machinery and innovation, Arthur Sleep shoes are made in our Savile Row workshop by skilled craftspeople, keeping London’s shoe traditions alive.
Thanks to the on-site microfactory filled with cutting edge machinery and a team of highly skilled artisans, customers can order at breakfast and receive by lunch. In the best Savile Row tradition, your shoes will be entirely personalised and made to measure, using a last made specifically and exclusively for them.
The Bespoke Shoemaking Process
Each of our Cordwainers (the traditional term for shoemakers) are trained in the entire shoemaking process, from measuring feet to the final polishing of the finished shoes.

01. Measurement
The process of creating a bespoke pair of shoes begins with an assessment of the customers feet. As each foot is invariably different, 3D scans and physical impressions in foam of both feet are taken. This process takes just two minutes to complete, and it allows our experts to assess how to make the shoes fit perfectly.
From the 3D scans and impressions, we create a custom pair of ‘lasts’. Lasts are the foot shaped moulds on which shoes are made, and they are crucial to getting the right fit and style of a shoe. Depending on which shoes have been ordered, we choose a last with a certain shape, and alter it to match the 3D scans and physical impressions of the customers feet.
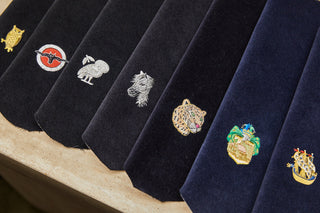
02. Design
Once we have the customers measurements, we can begin the design process.
After choosing one of our many styles, materials are selected for both the ‘upper’, the outside material, and the ‘lining’, the inside material. After the materials have been selected, the customer can choose details like a contrast colour binding, tassels or embroidery. This is where one can really have fun and create a truly unique look, as it’s the part of the process which is most customisable and individual to each person.
If a customer visits in store, they have the pleasure of feeling the actual leathers and fabrics we could use to make their shoes from, but we also have a Bespoke by Post service where we can take measurements by post and send leather and fabric swatches anywhere in the world.
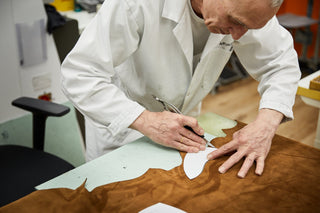
03. Clicking
The next stage is to prepare the materials for ‘clicking’ - this is the name of the cutting process.
All of the materials are cut to order, taking into consideration every special request of the customer and their unique feet.
Clicking is a very skilled job, to correctly cut shoe pieces takes years of understanding how leather and fabric move and behave, and how to get the best out of each skin or weave for each pair of shoes. The fact we cut each pair to order means we have the minimum waste possible, which means our shoemaking process is very sustainable.
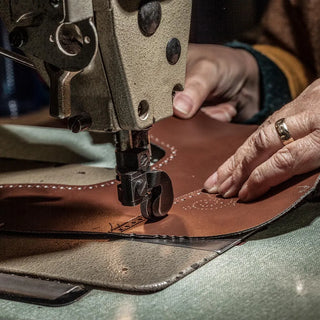
04. Closing
After the pieces are cut to the pattern, which has been specially adapted to the customers feet, they are sewn together on our specialist sewing machines. This process is called ‘closing’.
Sewing shoe uppers is similar to doing a 3D jigsaw puzzle, where the pieces are all different shapes and sizes and can easily move while you try to put them in place. Our very skilled cordwainers know just how to assemble each upper to create the most comfortable, sturdy and stylish shoes possible.
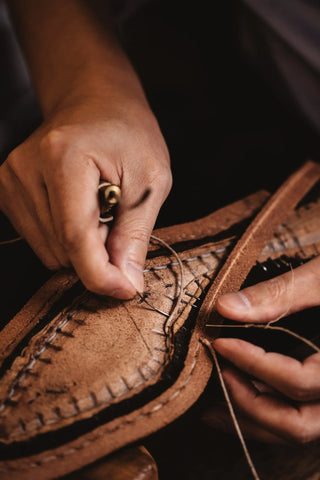
05. Making
Once the custom uppers are sewn together, the shoemaker can begin ‘making’ the shoes. Although the term ‘shoemaking’ is used to describe the whole process of creating a shoe, the term ‘making’ refers to the part of the process where the uppers are turned into shoes, as the customer would recognise them.
This involves pulling the uppers tightly over the customised lasts to give the shoes their shape, and adding stiffeners in the heel and toe areas before finally attaching the soles and heels.
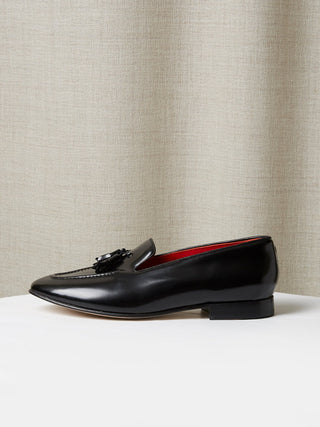
06. Finish
When the shoes are finished being ‘made’, they are given a final polish and checked over by our master cordwainers to ensure they are perfect. They are then presented to the customer, unique and perfectly fitting footwear in which to take on the world.